How TNB Reduced Warehouse Inventory Verification Time by 90x with Docked Drones in Malaysia
90%
Faster verification
2000+
Images processed daily
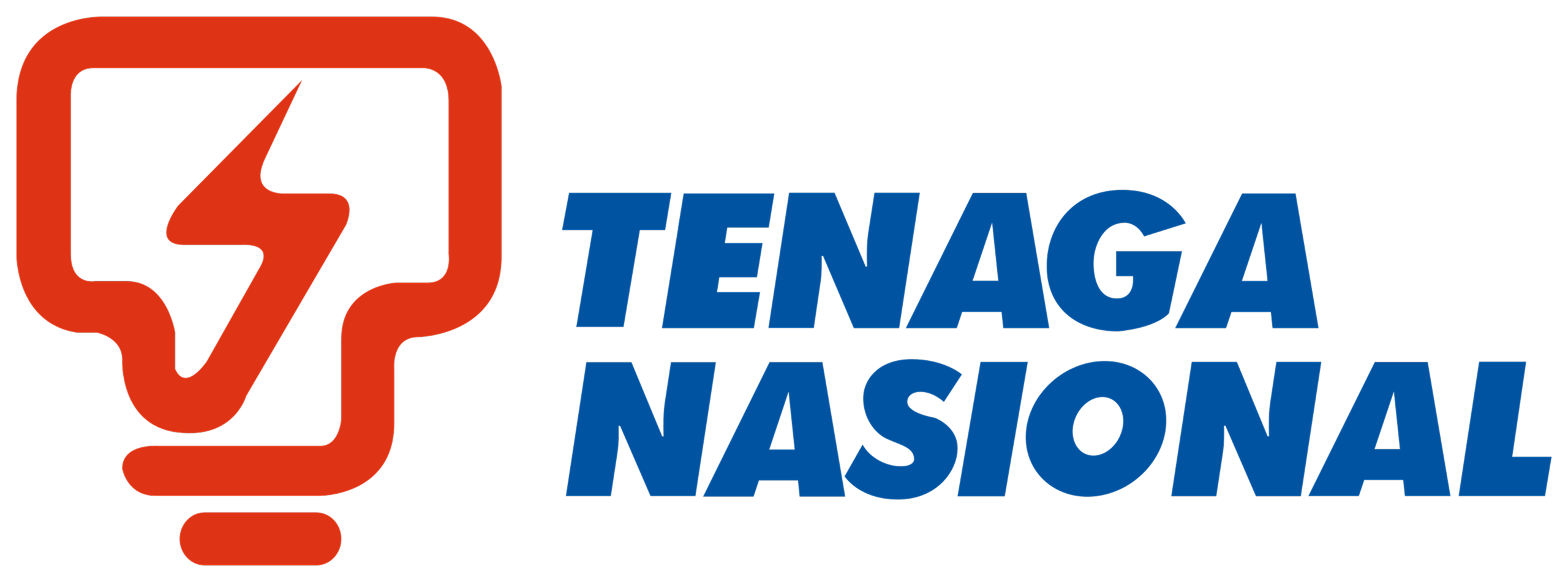
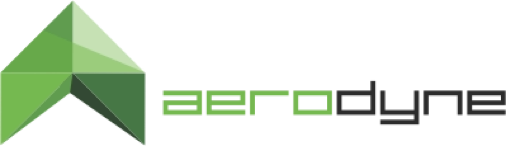
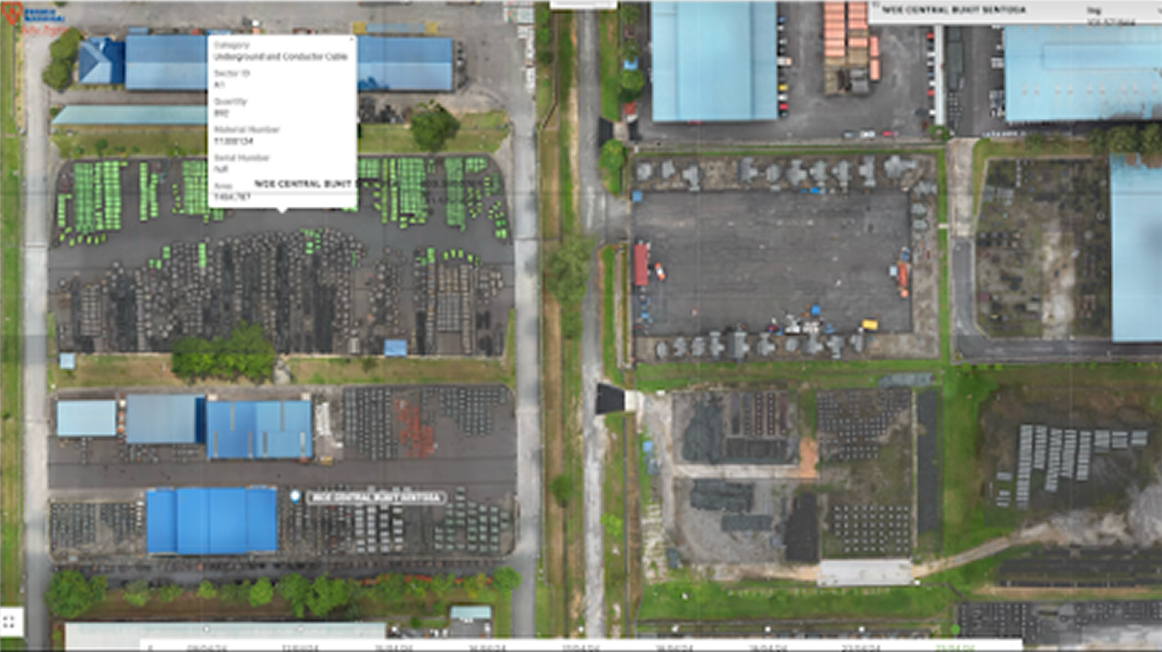
Tenaga Nasional Berhad (TNB) serves approximately 10 million households as Malaysia's primary energy supplier, operating an extensive network of distribution and transmission lines throughout Peninsula Malaysia. They also manage power exports to neighboring countries including Singapore and Thailand. As part of their technological transformation strategy, TNB sought efficient ways to monitor and manage their massive warehouse operations.
β
During one of the NestGen '25 sessions, we spoke with Azfar Helmi, Technical Product Manager in the Operations and Engineering department at Aerodyne Group, a global leader in drone technology and data analytics with presence in 45 countries. Azfar brings over nine years of experience in remote sensing with deep specialization in drone technology, particularly in shaping Aerodyne's nested drone initiatives in mining and energy sectors. Here's what they had to say about revolutionizing warehouse asset monitoring:
β
The Challenge
"Doing manual inspection would take a lot of time. In fact, when we spoke to our client initially back in 2023, the initial pain point was the time constraint because for each round of asset inspection, it would take them about three months to complete." - Azfar Helmi, Technical Product Manager, Aerodyne Group
TNB faced several critical challenges in managing their warehouse operations:
- Time-consuming inventory verification: Manual inspection cycles required three months to complete, rendering data outdated within days due to daily asset movement.
- Limited visibility in vast spaces: Operating a 43-hectare warehouse split between distribution and transmission assets made comprehensive monitoring nearly impossible through traditional methods.
- Space optimization difficulties: With large equipment like transformers and cable spools requiring significant storage area, TNB needed real-time insights about available space to maximize storage efficiency.
- Asset tracking accuracy: Daily movement of assets during regular business hours created persistent discrepancies between inventory records and actual warehouse contents.
The warehouse contained diverse electrical equipment including transformers, insulators, switches, and cable drums β all in varying quantities and dimensions. Traditional methods couldn't provide the speed, accuracy, or frequency needed to maintain effective inventory control in this dynamic environment.
β
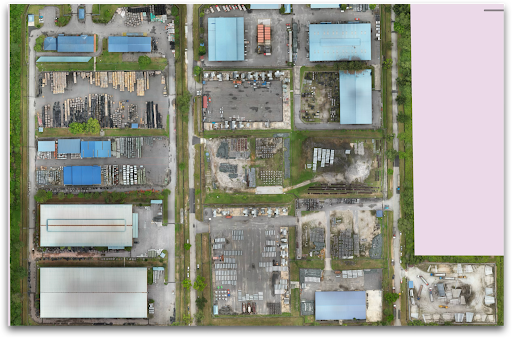
The Solution
In September 2023, TNB partnered with Aerodyne to implement an autonomous drone dock solution powered by FlytBase Enterprise. The system combines DJI dock technology with advanced AI analytics to transform warehouse asset management.
The implementation included:
- Installation of a DJI Dock utilizing a DJI Matrice 30 drone
- Starlink connectivity for reliable communications
- FlytBase Enterprise platform integration with AWS server infrastructure
- Custom AI algorithms developed specifically for electrical equipment detection and classification
- Specialized visualization software to present asset information in an accessible format
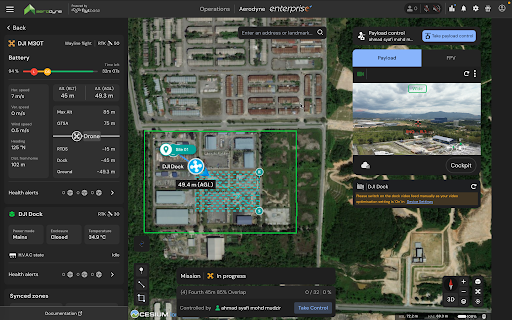
How it works
The autonomous drone system follows a systematic process to deliver actionable insights:
- The warehouse area is divided into five sectors for organized coverage
- The dock drone performs daily flights across all sectors (weather permitting)
- Approximately 2,000 images are captured during each complete mission
- All data is transferred from the FlytBase platform to AWS for processing
- AI algorithms analyze the images to detect, classify and quantify assets
- Visualization software presents the processed data to TNB's warehouse management team
- Results are delivered within 24 hours, enabling next-day planning decisions
The AI detection system is trained to recognize various electrical components with high accuracy, including transformers (95% accuracy), cable bundles (80-85% accuracy), and insulators (90%+ accuracy). The system can also identify empty spaces for inventory planning purposes.
Implementation
The implementation followed a careful, methodical approach beginning with system installation in October 2023. Rather than scheduling fixed flight times, the team adopted a flexible mission execution strategy to accommodate Malaysia's unpredictable weather patterns. On-site pilots remained on standby to manually execute missions when automated schedules were disrupted by rain or strong winds.
β
The most significant implementation challenge involved developing and refining the AI detection algorithms. Smaller components proved difficult to identify from mapping imagery alone, requiring additional training to estimate quantities in stacked configurations. Through iterative improvements, the team achieved the current 90% overall detection accuracy within months of deployment.
β
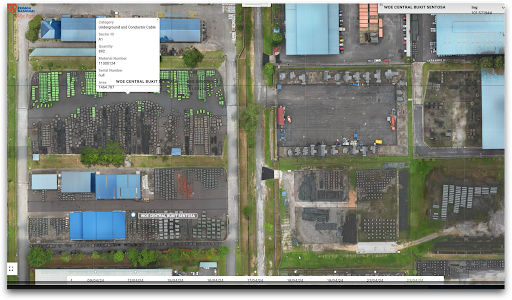
"We have been in touch with TNB for this specific project since September 2023. By October 2023, we deployed one DJI Dock in the TNB warehouse." - Azfar Helmi, Technical Product Manager, Aerodyne Group
Impact
The dock drone solution has delivered substantial operational improvements for TNB's warehouse management:
- Drastically reduced verification time: What previously took three months can now be completed daily, with results available within 24 hours β a 90-fold improvement in verification speed.
- Enhanced inventory visibility: Daily asset verification provides near real-time awareness of warehouse contents, including quantities, classifications, and precise locations of critical components.
- Optimized space utilization: TNB engineers now receive updated information about available storage areas every other day, allowing them to plan equipment deliveries and placements efficiently.
- Improved classification accuracy: The AI system can distinguish between different types of electrical components (transformers, insulators, switches, etc.) with up to 95% accuracy for certain equipment categories.
- Data-driven decision making: Warehouse managers can now make decisions based on current inventory status rather than outdated information, improving resource allocation and planning.
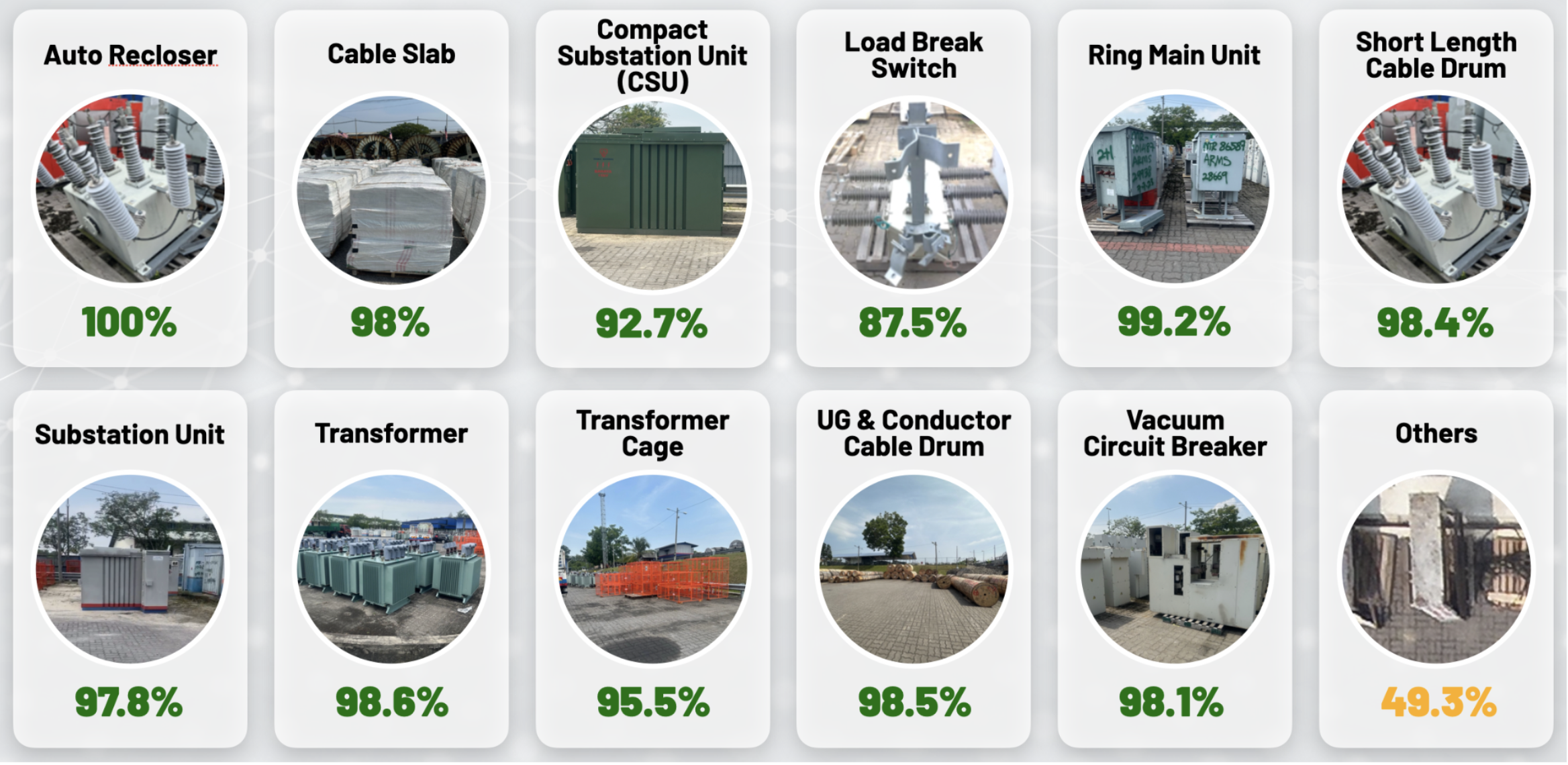
β
"Without AI, a normal person will have to go there and do individual verification, or even if you want to rely on mapping and let GIS analysts do the identification on a daily basis, one single map will take at least two weeks for classification. But with AI, we can take pictures today, and TNB will have the results by the end of the next working day. By the third day, they can use those insights already." - Azfar Helmi, Technical Product Manager, Aerodyne Group
Way Ahead
Following the success of the initial implementation, TNB is expanding the use of autonomous dock drone technology:
- Deployment of additional docks at the same warehouse location for security surveillance
- Planned expansion to other TNB facilities for comprehensive security monitoring
- Testing phase for dock deployment at electrical substations for weekly or monthly inspections
- Ongoing refinement of detection algorithms to improve accuracy for all equipment types
- Exploring potential indoor warehouse applications using SLAM and LIDAR technology
TNB's experience demonstrates the scalable nature of autonomous drone technology, with each successful application creating opportunities for expansion to additional use cases and locations.
Conclusion
The partnership between TNB, Aerodyne, and FlytBase demonstrates how autonomous drone technology can transform warehouse asset management in the energy sector. By reducing verification time from months to days, improving inventory accuracy, and enabling data-driven space optimization, the solution delivers immediate operational value while providing a foundation for ongoing innovation and expansion.
FAQ
Q1. What are the primary regulatory challenges for deploying dock drone systems in warehouse environments?
In Malaysia, obtaining approval for Beyond Visual Line of Sight (BVLOS) operations requires a rigorous five-month audit process with the civil aviation authority. Operators must demonstrate safety protocols, impact assessments, and continuous pilot awareness systems. Regulatory requirements vary by country, so consultation with local aviation authorities is essential before deployment.
β
Q2. How does AI-driven analysis improve the efficiency of drone-based warehouse monitoring?
AI transforms raw drone imagery into actionable insights by automating the identification, classification, and quantification of inventory items. Without AI, processing 2,000 daily images would take weeks of manual analysis. The AI system can process the same volume overnight, delivering results that are immediately useful for operational planning.
β
Q3. What accuracy levels can be expected from drone-based inventory detection systems?
Current systems achieve overall detection accuracy of approximately 90%, with variations by item type. Larger items like transformers reach 95% accuracy, while smaller or stacked items like cable bundles achieve 80-85%. Detection accuracy continues to improve through iterative AI model training with verified inventory data.
β
Q4. What is the recommended approach for scaling dock drone technology across multiple facilities?
Start with a single unit deployed for 3-6 months to evaluate operational value and integration challenges. Based on proven results, expand incrementally (3-5 additional units) while monitoring performance and value creation. This measured approach allows organizations to build internal expertise and develop optimal use cases before full-scale deployment.