Streamlining Infrastructure Inspections: The Power of AI and Docked Drones
Infrastructure inspections are essential for maintaining the safety of assets like bridges, dams, and power lines. However, traditional methods face many challenges, including safety risks, slow processes, and human errors. As technology evolves, automated docked drone workflows offer a more efficient, scalable, and safer solution.
In our recent Platform Connect webinar with Russ Ellis, President of gNext, we explored how Drone-in-a-Box (DiaB) technology will transform infrastructure monitoring and maintenance. This approach enables organizations to conduct frequent, precise inspections with reduced risk. In this blog post, we’ll highlight key takeaways from the webinar, discussing how automation is tackling the challenges of manual inspections and why DiaB technology is at the forefront of this shift.
Challenges with Manual Asset Inspections
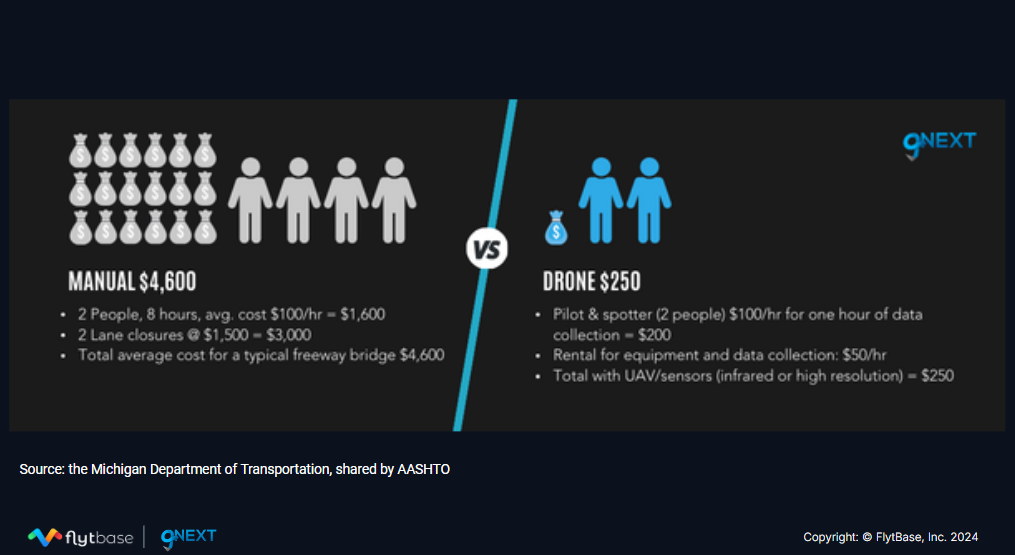
Manual inspections are expensive, inefficient, and often risky, requiring significant resources and time. For example, while a drone inspection costs approximately $250, including all resources, manual inspections can cost up to $4,600 due to additional labor and extended timelines (as shown in the image above). Inspectors frequently navigate challenging and hazardous environments, such as bridge tops or confined spaces like cooling towers, further complicating operations and increasing safety risks.
“As we know, manual asset inspections come with well-known challenges,” Russ remarked, “and safety is always top of mind and remains the highest priority.”
The lack of centralized information and reliance on manual data collection make it difficult to maintain consistent data quality, which in turn impacts decision-making and efficiency. This makes it harder to get a complete and accurate picture of an asset’s condition, potentially leading to costly repairs down the line if critical issues go undetected.
Streamlining Infrastructure Inspections with Drone Docks and AI-Driven Defect Detection
The Drawbacks of Manual Drone Operations
While drones have significantly enhanced infrastructure inspections, manual operations come with their own set of challenges. Frequent travel to remote inspection sites substantially increases overall inspection costs. Many facilities that need inspection are located in hard-to-reach areas, necessitating long-distance travel for pilots, which adds expenses for both travel and accommodation.
This logistical burden makes data collection more expensive and renders frequent inspections time-consuming, ultimately affecting the efficiency of inspection operations. Furthermore, scaling manual operations across multiple sites proves challenging, as it requires large teams of pilots and incurs high operational costs.
Streamlining Infrastructure Inspections with Drone Docks and AI-Driven Defect Detection
Overcoming Asset Inspection Challenges with Drones and AI
Fully autonomous docked drone systems allow drones to launch, conduct inspections, return for recharging, upload collected data and process the data; all without the need for human intervention. The drones are housed in docking stations on-site, ready to perform regular, scheduled inspections or be deployed in response to urgent issues.
Infrastructure inspection using Drones and AI can be implemented by:
- Determining the use-case
- Selecting suitable hardware and payloads
- Using a drone autonomy platform for data collection
- Selecting a data processing platform
Determine the Relevant Use-Case
The first step in any drone deployment project is to clearly define the use case. This involves identifying the specific tasks or challenges that the drone will address. For instance, in the infrastructure sector, drones can be used to:
- Inspect power lines: Identify potential hazards, assess damage, and plan maintenance.
- Monitor construction sites: Track progress, identify issues, and ensure safety compliance.
- Inspect bridges and dams: Detect structural damage, corrosion, and erosion.
- Survey disaster zones: Assess damage, locate survivors, and plan relief efforts.
.png)
Selection of Suitable Hardware and Payloads
With a wide range of options available, choosing compatible hardware is key. For instance, if a user operates an M300 or M30 drone, options like the Aisha Docking Station offer reliable charging support for these models. For those in the U.S. using an Anzu Raptor, Hextronics provides partner docking stations like the Hextronics Universal, designed to support Anzu drones. The Hextronics Atlas, compatible with M300 and M350 drones, even offers a battery-swapping capability to reduce operational downtime. DJI docks, widely adopted by enterprises for various use cases, also support the M30 series and M3T drones, adding versatility to drone operations.
Data Collection Made Easy with FlytBase
Infrastructure managers utilizing Drone-in-a-Box (DiaB) systems can efficiently automate inspections through mission planners and schedulers. Drones can autonomously take off, gather data, and upload it for analysis. Additionally, FlytBase facilitates live mission recording, allowing users to manually guide drones and register waypoints for future inspections.
“Each day at 9 AM, the drone autonomously takes off, collects all necessary data and media, and uploads it directly to the processing platform for further analysis through FlytBase.” said Ajinkya, Business Developement Lead, FlytBase.
This inspection workflow automation ensures consistent, high-quality data collection along the pre-programmed flight paths, capturing the same imagery each time for accurate comparisons. As a result, subtle changes that might be overlooked during manual inspections can be easily detected over time. Post-flight, the platform simplifies data management and export, making it easy to analyze inspection results on data processing platforms like gNext, etc. using FlytBase Flinks.
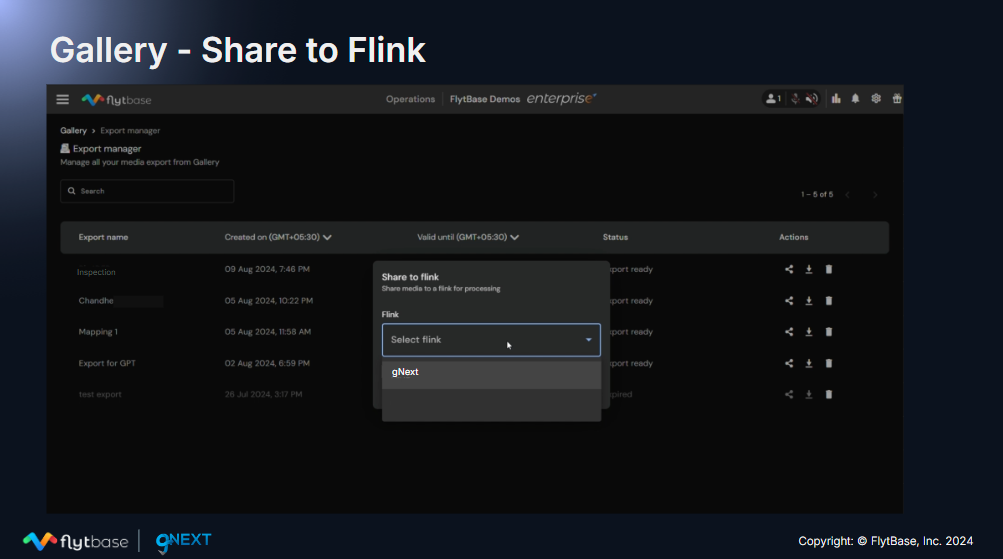
Russ shares, “We currently monitor 42 asset types, including various bridge types, dams, electric substations, nuclear power facilities, and cooling towers. From buildings and rooftops to cell towers—anything in the built environment—we either have it covered or soon will.”
Efficient data processing is crucial for asset inspections, and AI is pivotal in simplifying and enhancing this process. Softwares like gNext empower operators to select from over 42 predefined asset types and utilize AI-powered InspectAssist™ to detect and quantify defects in concrete structures.
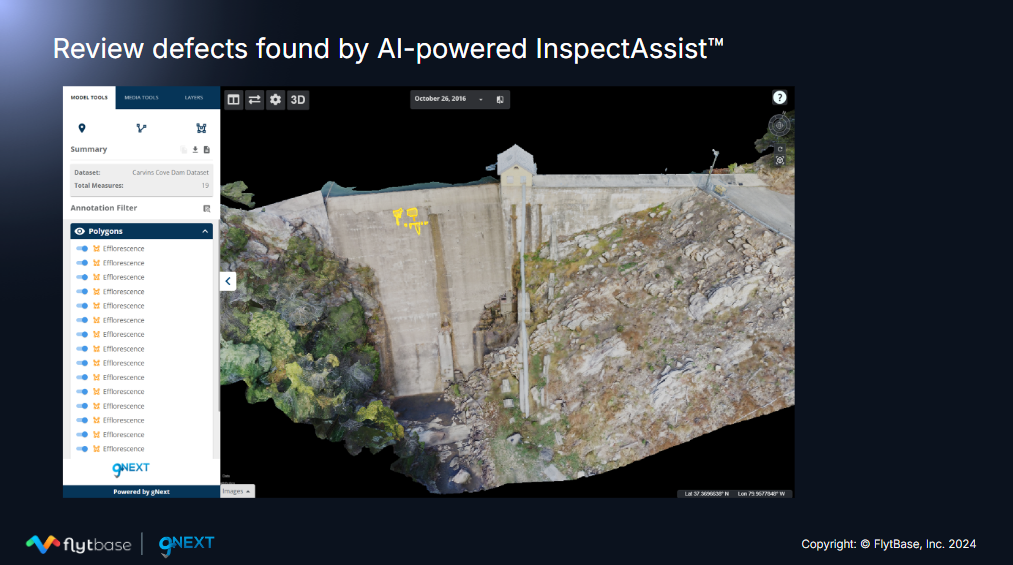
This streamlined approach enables informed decision-making within a single interface, significantly speeding up the inspection process while improving accuracy and reducing the risk of human error. With features like PlanView, Elevation, 2D/3D, Contour, Point Cloud, and DTM models, gNext offers a comprehensive inspection solution that scales with the needs of any project.
Conclusion
The integration of Drone-in-a-Box (DiaB) technology and data processing software like gNext into FlytBase’s platform is setting a new benchmark for infrastructure inspections. By eliminating the inefficiencies of manual methods and leveraging the power of automation, organizations can conduct inspections faster, safer, and with greater precision than ever before.
To learn more, watch our latest webinar on “Streamlining Infrastructure Inspections with Drone Docks and AI-Driven Defect Detection” with gNext here.
Get Your Free Drone Autonomy Guide Today!
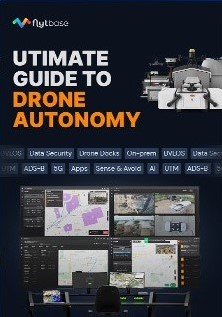